W branży farmaceutycznej opakowania odgrywają ważną rolę w zapewnianiu bezpieczeństwa, integralności i zgodności produktów. Jednym z kluczowych aspektów tego procesu jest co-packaging, termin często przeplatany, ale różniący się od co-manufacturingu. Omówmy, czym jest co-packing, jego niuanse, znaczenie w branży farmaceutycznej i czym różni się od co-manufacturingu.
Definicja co-packingu
Co-packaging refers to the process of assembling a product into its final packaged form. This process is crucial for pharmaceuticals, as it involves not only placing the product into its container (like a blister pack) but also ensuring that the packaging meets strict industry standards for safety and compliance. Co-packaging often involves the use of various packaging solutions, such as blister packs, capsule sizes, and compliance packaging, to ensure product integrity and patient safety.
Expanding beyond pharmaceuticals, co-packing serves industries like food and beverage, cosmetics, and consumer goods. For instance:
- Food and beverage: Co-packers enable companies to bottle, label, and package drinks or processed foods while ensuring regulatory compliance and quality.
- Cosmetics: Specialized packaging enhances the aesthetic appeal and marketability of cosmetic products.
- Consumer goods: Efficient co-packing solutions help companies meet seasonal demand spikes or scale product lines without the need for costly infrastructure.
Co packing vs. co manufacturing: Zrozumienie różnicy
While co-packing focuses on the final steps of assembling and packaging a product, co-manufacturing encompasses the entire production process, including formulation and packaging. For instance:
- In co-manufacturing, multiple parties may collaborate to produce a pharmaceutical product, such as formulating tablets, softgels, or capsules, before packaging them.
- Co-packing, on the other hand, strictly handles the final assembly and ensures compliance with packaging standards.
This distinction is vital when considering a strategic partnership, as companies need to align their specific needs with the services provided by their chosen partner.
Znaczenie opakowań zbiorczych w branży farmaceutycznej
Co-packaging is more than assembling products into their retail-ready form; it represents a critical step in maintaining brand integrity, regulatory compliance, and product safety. In pharmaceuticals, blister packaging machines ensure dose accuracy, tamper evidence, and product freshness. Similarly, in food and beverage, co-packers use advanced sealing machines topreserve quality and extend shelf life.
Key benefits of co-packing include:
- Cost efficiency: By outsourcing packaging needs, companies eliminate investments in specialized equipment, facilities, and workforce.
- Scalability: Co-packers allow businesses to scale operations seamlessly, handling seasonal spikes or large orders without disruption.
- Time savings: Delegating packaging responsibilities frees companies to focus on product innovation, marketing, and customer engagement.
- Regulatory compliance: Co-packers bring expertise in meeting industry-specific regulatory requirements, ensuring high standards in safety and quality.
Innowacyjne rozwiązania w zakresie opakowań zbiorczych
Advancements in technology have revolutionized co-packaging, enabling eco-friendly and customer-centric solutions. Some notable innovations include:
- Eco-friendly packaging: Recyclable plastics and biodegradable materials help brands align with sustainability goals.
- Child-resistant designs: Solutions like Locked4Kids ensure safety and compliance with regulatory standards.
- Automation: Blister packaging machines and automatic sealing equipment increase precision and efficiency, reducing errors and ensuring consistency.
By leveraging these technologies, co-packers not only streamline packaging processes but also enhance product appeal and functionality.
Addressing challenges in co-packing
While co-packing presents numerous advantages, companies may face challenges, such as:
- Communication breakdowns: Effective collaboration requires clear and consistent communication to ensure timelines and specifications are met.
- Limited scalability: Some co-packers may lack the capacity to support a rapidly growing business. Vet partners thoroughly to ensure alignment with future goals.
- Regulatory complexity: Navigating compliance requirements can be daunting; selecting a co-packer with proven expertise mitigates this risk.
By proactively addressing these challenges, businesses can maximize the benefits of co-packing while maintaining seamless operations.
Selecting the right co-packer
Choosing the right co-packing partner is critical for ensuring a successful collaboration. When evaluating co-packers, consider the following factors:
- Scalability and flexibility: Look for a partner capable of adapting to your evolving needs, whether it’s scaling production or handling diverse product lines.
- Certifications and compliance: Ensure the co-packer meets regulatory standards (e.g., GMP, ISO certifications) and possesses relevant industry expertise.
- Quality assurance: Verify the partner's quality control measures to maintain product integrity and consumer trust.
- Technological capabilities: Choose a co-packer equipped with state-of-the-art machinery and innovative solutions tailored to your product requirements.
For pharmaceutical companies seeking precision and reliability, Ecobliss’ GMP-certified rooms and tailored solutions offer a trusted partnership to meet your unique needs. Whether you’re scaling operations or enhancing compliance, co-packing with Ecobliss ensures your brand thrives in a competitive market.
Zamów bezpłatną próbkę już teraz!
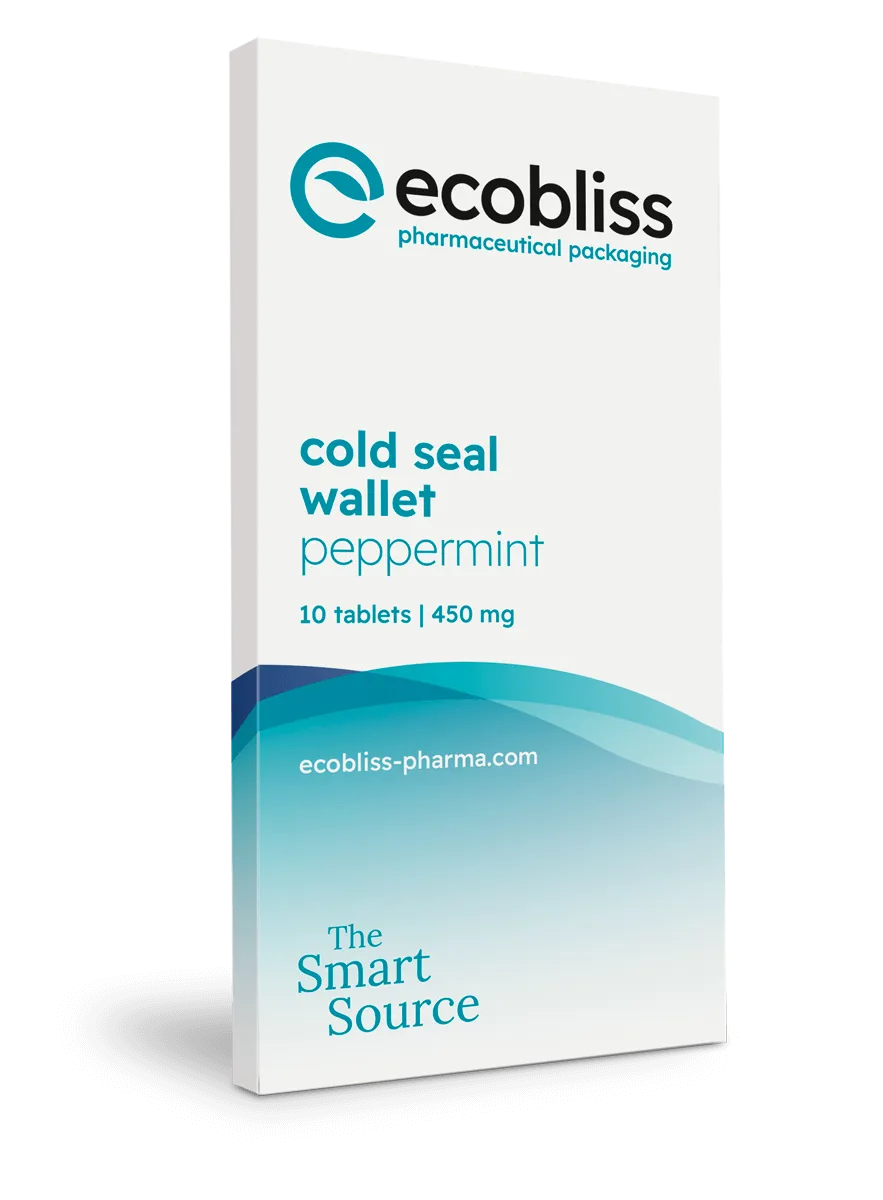