Design elements
The unit volume of a product's packaging determines the most suitable production process. For smaller volumes, manual or semi-automated filling processes may be more practical. In these cases, packages are designed to accommodate slower production speeds, with people manually assembling and filling them, often using small equipment for assistance. In contrast, packaging for high-volume products must be designed for fully automated machinery, allowing for faster and more efficient production.
Tip: Plan your design with flexibility in mind. By considering both manual and automated processes from the start, you can avoid costly design revisions as your production volume scales up.
Converting machinery and tooling
Choosing the right machinery is another critical aspect of packaging planning. Customized packaging requires specific machinery setup and production times, which directly affect costs. Knowing the anticipated volume—whether it's 50,000, 250,000, or 1 million units—allows the packaging supplier to choose the appropriate machinery with the best throughput rates. Different machinery sizes and speeds are used for varying production volumes, ensuring that the process is optimized for both cost and efficiency. Tooling, such as molds or die cuts, is also laid out based on volume forecasts, further enhancing production efficiency.
{{cta-sample-request}}
Level of automation for packaging filling
The level of automation in the packaging process is a crucial factor in maximizing profitability. Depending on your forecasted volume, the packaging process could range from manual to fully automated. Factors such as available equipment, budget, and confidence in product growth influence the decision. Sharing your strategic vision with your packaging supplier allows them to tailor the design, tooling, and equipment to your specific needs. This foresight helps prevent the need for redesigns or tooling replacements as your product scales, minimizing the risk of costly structural changes.
Tip: Packaging planning early on can save you from unexpected costs later, particularly if your sales outpace your initial packaging setup.
Early cost estimate requests
Early in your project, obtaining cost estimates - even with uncertain volume projections - is crucial. These estimates help determine the feasibility of your chosen packaging format and guide important decisions about design, materials, and production processes. Customized packaging components involve various variables that can significantly impact costs, such as material choice, machinery type, and automation level. Understanding these factors early on allows you to design an efficient and cost-effective packaging solution tailored to your production needs.
Collaboration with a trusted supplier
Thoughtful packaging planning ensures a functional, scalable, and cost-effective solution for your product. By accurately estimating your packaging volume, selecting the right machinery, and planning for both current and future needs, you can avoid unnecessary complications and reduce costs. A carefully planned packaging strategy will deliver long-term results and support your business’s growth.
Contact us today to learn how thoughtful packaging planning can optimize your prodution process and drive long-term success.
Request a free sample now!
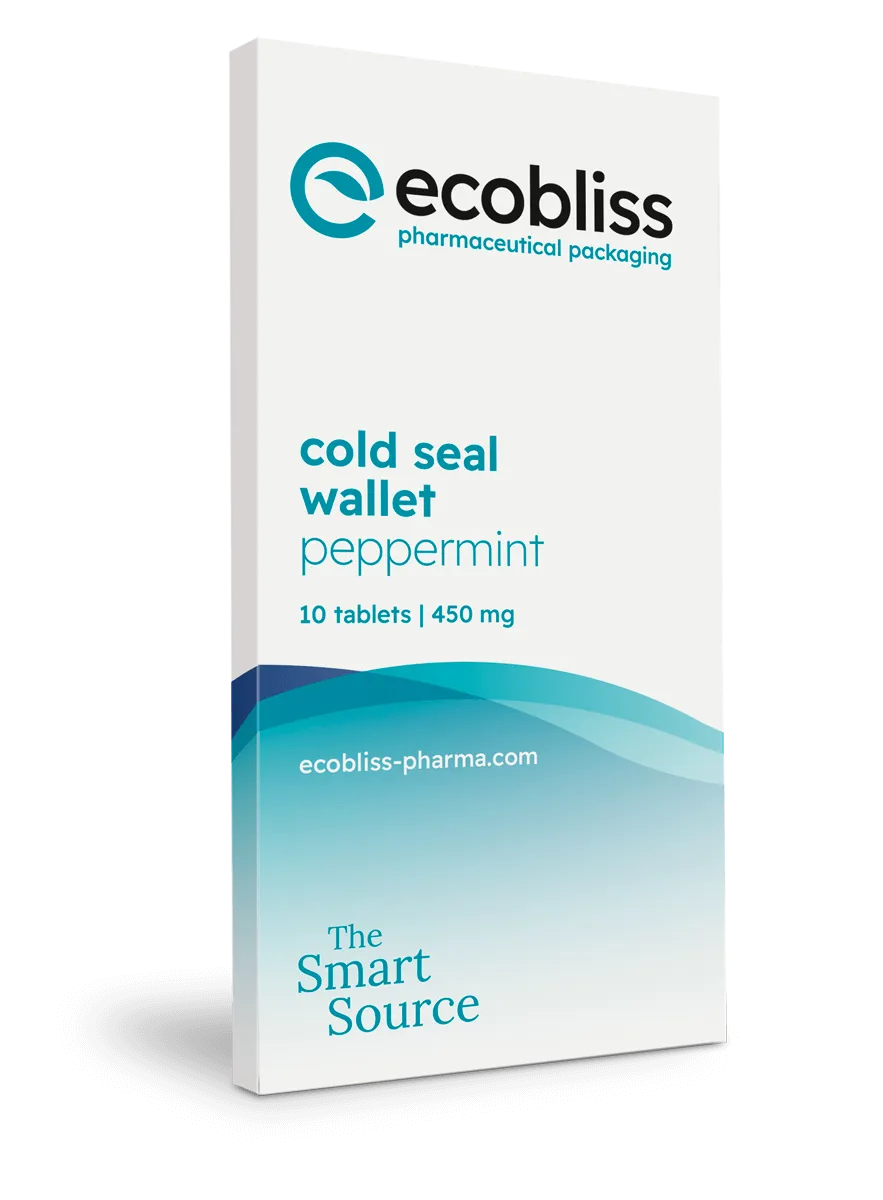