Tablet coating machines are pivotal in pharmaceutical production, serving not just to enhance the visual appeal of tablets. They also protect the active ingredients, mask unpleasant tastes, and control drug release. This dual role of aesthetic enhancement and functional protection underscores their value in the manufacturing process. In this blog, we will help you answer the question ‘what is a tablet coating machine’, as well as show you the different types and advantages.
Evolution of tablet coating techniques
The journey from traditional sugar coating to contemporary film coating reflects significant advancements in efficiency, functionality, and patient compliance. Sugarcoating, while effective for taste masking, was labor-intensive and time-consuming. The shift to polymer-based film coatings revolutionized the industry by offering thinner, more uniform coatings. These could be tailored to achieve specific release mechanisms and improve drug stability.
Operational principles of a tablet coating machine
Thus, what is a coating machine exactly? The core function of a coating machine involves applying a uniform coating to tablets under controlled conditions.This process typically includes loading the tablets into the coating drum, spraying them with a coating solution, drying the tablets to fix the coating, and unloading them for packaging. Achieving a uniform coat requires precise control over the spray rate, drum speed, and drying temperature.
Types of tablet coating machines
There are several types of coating machines, each with its unique features and advantages.
· Pancoaters: Traditional machines of the tablet coating process, pan coaters rotate a pan or drum to tumble tablets while coating them with a spray solution. They are celebrated for their simplicity and effectiveness in batch processing.
· Perforated drum coaters: This is an evolution of pan coaters. These machines feature a perforated drum that improves air flow and drying efficiency. This leads to faster processing times and more consistent coatings.
· Fluid bed coaters: Representing a significant technological leap, fluid bed coaters use a fluidization process to suspend tablets in air. This allows for even coating and efficient drying. It is a method that is particularly suited for fine-tuning the coating process to achieve specific release profiles.
Advantages of a modern coating machine
The adoption of an advanced type of tablet coating machine offers several compelling advantages:
· Efficiency: Enhanced processing speeds and automation reduce production times and labor costs.
· Consistency: Improved control mechanisms ensure uniform coating thickness and quality across batches.
· Versatility: Ability to accommodate a wide range of coating materials and tablet sizes. Explore the importance of qualitative pharmaceutical packaging materials.
· Compliance: Modern coating machines are designed to meet stringent regulatory standards for safety and quality.
What is challenging for a tablet coating machine?
Despite technological advancements, tablet coating remains a complex process with inherent challenges:
· Uniformity: Achieving consistent coating thickness and quality across all tablets in a batch can be difficult.
· Adherence: Ensuring the coating material adheres properly to the tablet surface without causing defects requires precise control of the coating conditions. Especially with today's wide array of tablets.
· Scalability: Transferring coating processes from pilot scale to full production scale without loss of quality demands thorough understanding and careful adjustment of process parameters.
Coating machines’ impact on controlled release and patient compliance
Coating technology is important in developing controlled-release formulations that deliver medication at the desired rate, improving therapeutic outcomes and patient adherence. Coatings can also be used to differentiate products, provide information, and improve the overall patient experience through enhanced visual appeal and taste masking.
Looking ahead: innovations in tablet coating technology
The future of tablet coating technology is marked by innovation. Ongoing research focuses on developing new coating materials, enhancing process control, and integrating smart technologies for real-time monitoring and optimization. These advancements promise to further improve the efficiency, flexibility, and environmental sustainability of tablet coating processes.
So, the answer to the question ‘what is a tablet coating machine’ is hopefully clear now. Each coating machine plays a crucial role in pharmaceutical manufacturing, combining aesthetics with important functional benefits. As the industry keeps changing, these machines will remain at the forefront of technological advancements. This drives improvements in drug delivery, patient compliance, and manufacturing efficiency. Their development reflects the pharmaceutical industry's ongoing commitment to quality, innovation, and patient care.
Request a free sample now!
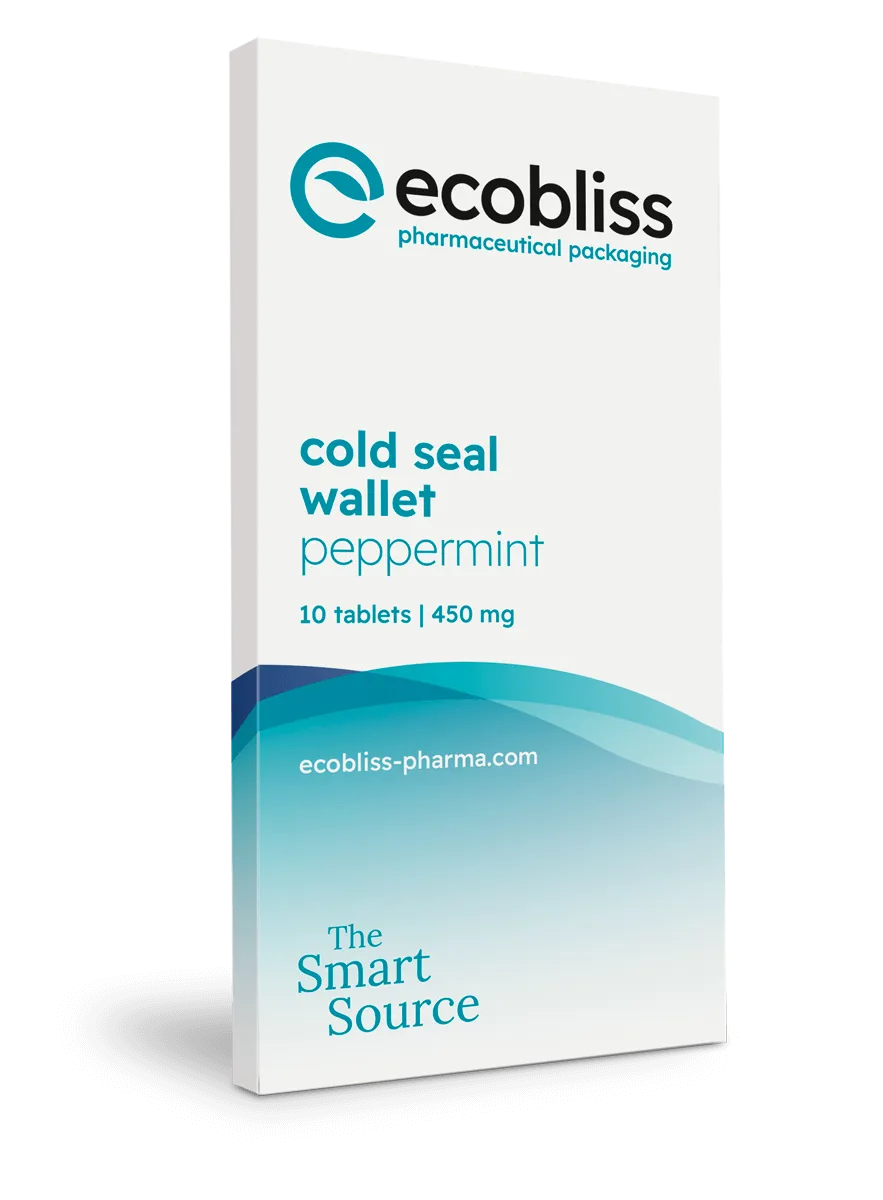