Thermoforming is a manufacturing process widely utilized across various industries, but it's particularly significant in pharmaceutical packaging due to its versatility and efficiency. This method involves heating a plastic sheet until it’s formable, then forming it over a mold to achieve a desired shape. Once cooled, the plastic retains the mold’s shape, and excess material can be trimmed away, resulting in a high-quality product ready for use.
The thermoforming process: A blend of art and science
The elegance of thermoforming lies in its simplicity and its sophistication. Here's how thermoforming works:
- Heating the plastic sheet - The journey begins with heating a flat plastic sheet to a temperature where it becomes soft and malleable.
- Molding - The warm plastic is then draped over a mold. This can be done using vacuum forming, where a vacuum draws the plastic against the mold, or pressure forming, where air pressure is applied.
- Cooling and trimming - After the plastic has conformed to the mold, it's cooled down to solidify into the new shape. The final step is to trim the excess material, which can often be recycled.
Why thermoforming is pivotal for pharmaceutical packaging?
Pharmaceutical packaging requires a method that is not only cost-effective, but also capable of producing reliable and consistent results that meet stringent industry standards. Thermoforming checks these boxes and offers several key advantages:
- Precision and customization - Thermoforming allows for precise control over the thickness and details of the packaging. This is crucial in pharmaceuticals, where the dosage and integrity of medication must be protected.
- Material efficiency - With advanced trimming and recycling capabilities, thermoforming is a friend to companies conscious of their environmental footprint.
- Protective qualities - The packaging created through thermoforming can be designed to be child-resistant, aligning with the best practices of safety and compliance.
The sustainable edge of thermoforming in pharma
Sustainability is a growing concern in all sectors, including pharmaceuticals. Thermoforming aligns with green initiatives by reducing waste during production. Moreover, advancements in bio-based plastics are opening new doors to eco-friendly packaging options, contributing to a circular economy. Learn more about sustainability in the pharmaceutical industry.
The potential of thermoforming
A common question in the manufacturing industry is “What is thermoforming (plastic)?”. However, understanding the complexities of thermoforming is just the beginning. If you're looking to explore how this process can be of value in your pharmaceutical packaging, or if you need assistance in developing a packaging solution that meets the exacting standards of the industry while upholding the values of safety, compliance, and environmental responsibility, reaching out for expert guidance is the next step.
For further information on how thermoforming can be integrated into your packaging strategy, or to request a sample of cutting-edge packaging solutions, do not hesitate to get in touch. Our door is always open to assist you in navigating the packaging landscape and identifying the solutions that best fit your needs.
Request a free sample now!
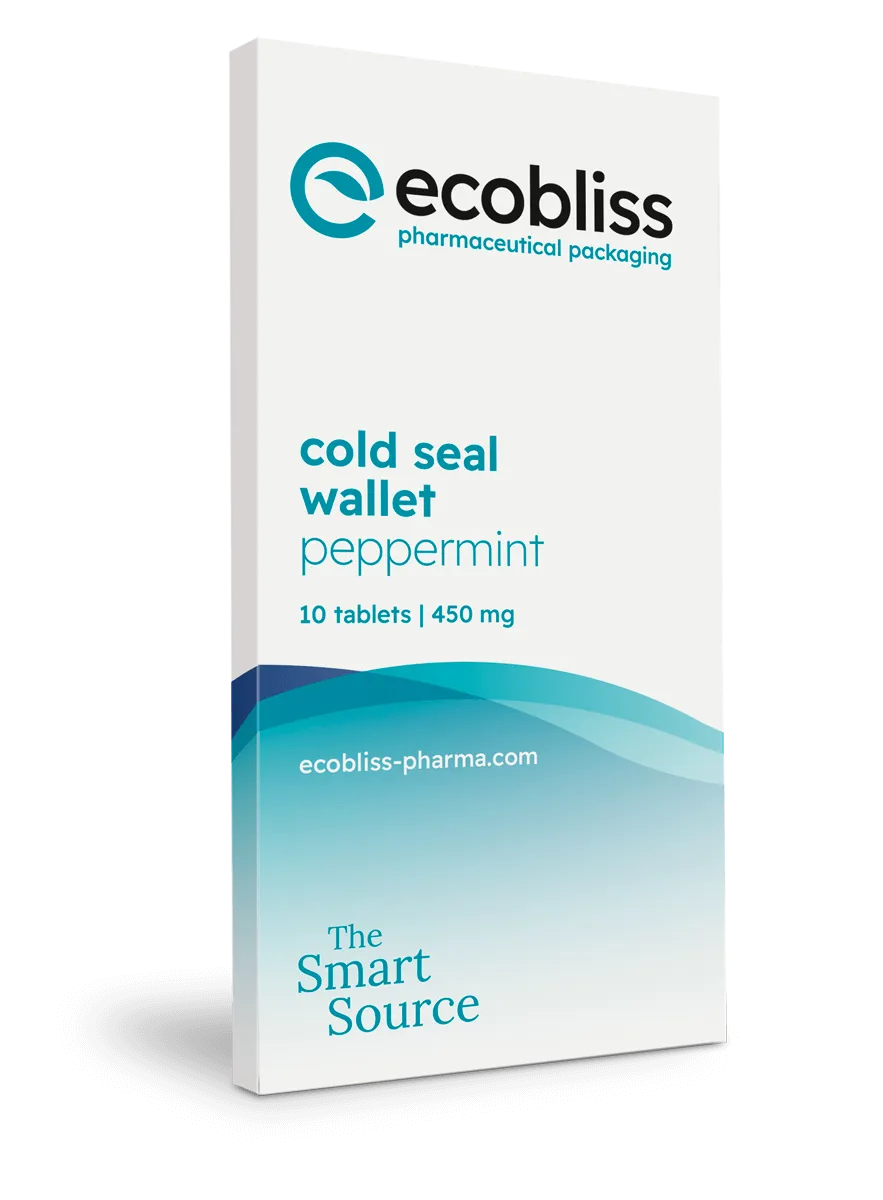