Validation in the pharmaceutical industry is a critical procedure that ensures the safety, quality, and efficacy of drugs. Required by regulatory bodies such as the FDA, EMA, and WHO, validation is a cornerstone of pharmaceutical manufacturing, offering documented evidence that processes operate as intended. This article will define process validation and its practical applications in the pharmaceutical industry.
How to define process validation?
Validation is the process of generating documented evidence that a specific procedure, process, or activity consistently leads to the expected results. It is essential for ensuring product safety and compliance with guidelines such as ICH guidelines for process validation and WHO guidelines for validation.
Process validation is not just about meeting legal requirements; it is a proactive quality assurance measure that prevents issues like cross-contamination and product failure, thereby protecting public health and maintaining trust in pharmaceutical products. There are different types of pharmaceutical process validations, which we will elaborate further on.
Types of validation in pharma
1. Process validation
This type confirms that the manufacturing process produces outputs that meet predefined specifications. It is conducted in three stages: process design, process qualification and continued process verification. This is a fundamental requirement outlined in FDA’s Current Good Manufacturing Practices (cGMP).
2. Cleaning validation
This ensures that cleaning methods effectively remove residues, contaminants or microorganisms from equipment to prevent cross-contamination. Cleaning validation is particularly critical for multi-product facilities.
3. Analytical method validation
Verifies the accuracy, specificity, reproducibility and robustness of methods used to test pharmaceutical products. Compliance with ICH Q2(R2) is required for this process.
4. Equipment validation
Confirms that equipment operates consistently within required parameters and supports the production of quality products. This includes qualification stages such as Design Qualification (DQ), Installation Qualification (IQ), Operational Qualification (OQ), and Performance Qualification (PQ).
Often, the terms qualification and validation are used inter. However, they servedifference purposes in pharmaceutical manufacturing.
- Qualification focuses on ensuring that equipment, systems, or facilities function as expected. This includes activities such as Design Qualification (DQ), Installation Qualification (IQ), Operational Qualification (OQ), and Performance Qualification (PQ).
- Validation, on the other hand, has a broader scope. It ensures that the entire process, including equipment, systems, and methods, consistently produces a product meeting predefined quality standards.
This distinction is crucial for understanding the steps involved in ensuring product quality and compliance with regulatory requirements.
The steps of process validation
Validation in the pharmaceutical industry typically follows a systematic approach:
- Design qualification (DQ)
This initial step ensures that the proposed design of the equipment or process meets the requirements for the intended purpose.
- Installation qualification (IQ)
In this phase, it's confirmed that the equipment or systems are installed correctly and according to the manufacturer's recommendations.
- Operational qualification (OQ)
Here, it's determined whether the systems and equipment operate according to the intended operating ranges.
- Performance qualification (PQ)
The final step involves testing that the equipment consistently performs according to the process parameters and can produce the desired output.
The importance of a systematic approach
A systematic approach to validation is crucial because it helps identify potential variability in processes and establishes measures to control these variables. This is not just about ticking off a compliance checklist; it's about guaranteeing the quality and consistency of life-saving drugs in qualitative healthcare packaging. This includes ensuring secure and tamper-evident solutions such as blister packs for medication, which protect dosage integrity and enhance patient safety. That's why EcoBliss is your partner in healthcare packaging
Validation and its role in quality assurance
Validation is an integral part of Quality Assurance (QA) in the pharmaceutical industry. It's a proactive measure that identifies potential problems before they affect the final product. It is a preventive approach rather than a reactive one, saving companies from costly recalls and maintaining their reputation.
The regulatory environment
There quirement for validation is grounded in regulations such as the FDA's Current Good Manufacturing Practices (discover why GMP matters, the European Medicines Agency's (EMA) guidelines, and the International Council for Harmonisation of Technical Requirements for Pharmaceuticals for Human Use (ICH)guidelines.
Validation in action
To bring the concept of validation to life, let's look at a real-world application. In a packaging context, consider the Locked4Kids Wallet Box: a child-resistant solution. Before this innovative packaging hits the market, it undergoes rigorous testing and validation to ensure it meets safety standards while being accessible to adults. This kind of validation includes tests to verify that the packaging is tamper-evident, durable, and functions as intended.
The need of continuous validation
Validation is not a one-time event but a continuous process. As new data are gathered, processes might be refined, and validation activities will be carried out again to ensure continuous compliance and quality.
Challenges and considerations
Validation can be complex, and some of the challenges include integrating new technologies, adapting to evolving regulations, and managing the costs associated with validation activities.
It’s a vital part of the pharmaceutical industry's commitment to delivering safe and effective products and a dynamic process that requires attention to detail, a thorough understanding of processes, and a commitment to quality. Understanding the importance of validation is essential for anyone involved in the pharmaceutical industry, from the lab to the boardroom.
Want to discuss how a robust validation process can be implemented for your pharmaceutical products? Don't hesitate to reach out. Our team is ready to provide expert guidance and support, ensuring your products meet the highest standards of quality and safety.
Request a free sample now!
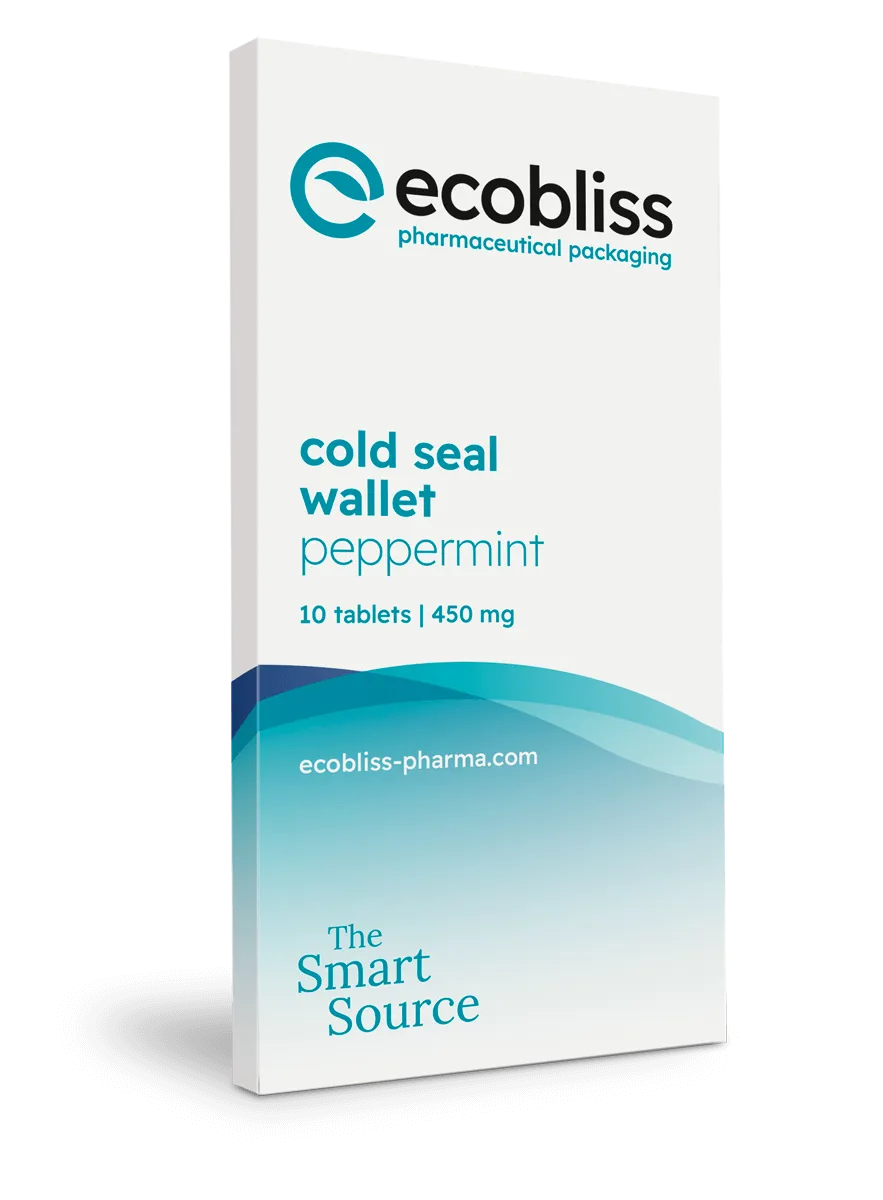